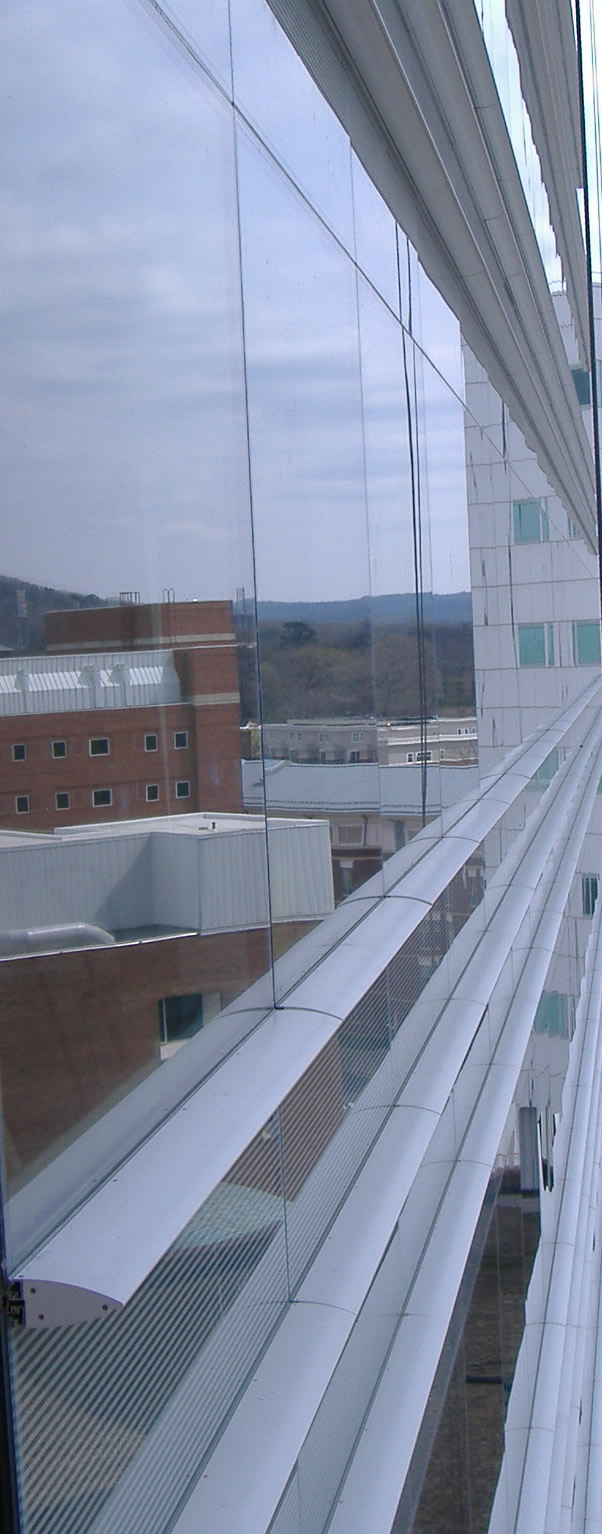
|
Building Statistics II |
Construction |
The Hospital Bed Expansion is located on the Univeristy of Virginia Campus in Charlottesville, VA. This expansion will boast 60,000 square feet of new space for patient rooms and 60,000 squre feet of renovated space that will connect to the patient area. The expansion will add six floors for occupied patient space with seven patient rooms on each floor; additional space will be added to the second floor mechanical room (floor 2M). A new penthouse will also be added to the new expansion, bringing the total building height to 652' - 0" at the high roof level. The current estimated cost of this project is $55 million with an expected completion date of April 2012.
This project is being constructed under a Multiple Prime contract being held by the University of Virginia (UVA). Under this type of arrangement, every individual subcontractor will have a contract that is held by the owner rather than a construction management (CM) firm. Along with owner holding each subcontractor's contract, UVA also holds the CM Agency's contract. Gilbane and Russell have entered into a joint venture to act as the CM Agency for the Hospital Bed Expansion (HBE).
While HBE is being constructed, UVA also has two other project in progress in the same area as HBE. The Emily Couric Cancer Center (ECCC) is adjacent to this project and will begin construction around the same time frame as HBE. Before ECCC can be built, an existin gparking garage will need to be demolished, causing complications for the Lee Street traffic pattern. Towards the end of the Cancer Center construction, another project will be starting up, Connective Elements. The "Connective Elements" mission is to create a transportation hub that will seemingly connect the Lee Street Parking garage, University Hospital, and Emily Couric Cancer Center. The issue with all of these project occuring at the same time is that lay out space will be severely limited for each project. The sit plan for this project is small and throughout the project this small area will become extremely congested with the addition of trades being on site. Because there is a very limited amount of space for staging areas, steel cannot not be brought to the site early. Also, because of the congested traffic patterns (both pedestrian and vehicular) the erection of steel will take place in the evenings. The erection of the superstructure will coincide with the pre-sequenced steel pieces being transported to the project each corresponding evening.
Because construction is being done to an occupied hospital, it is critical that the safety of patients, visitors, and staff take priortiy amongst all concerns of the construction management team. The alrgest risks take shape in the form of Infection Contrl and Interim Life Safety Systems. In order to reduce teh risk of disrupting these systems and/or creating dangerous situations involving dust or heat, the management team used stringent requirements that mandated the us of Directive No. 723A/902A which outlines the health safety requirements for construction in occupied hospital facilities. This directive led to the installation of temporary ICRA walls which also were designed with a 1-hour fire rating. Along with the installation of ICRA walls, the project was subject to scheduled and random inspections to ensure that all requirements were being met. |
Mechanical |
Other than two new air handling units on the Penthouse Roof Level, the mechanical system does not undergo much of a major addition. The Penthouse will accept two new variable air volume (VAV) air handling units (AHU) with a capacity of 70,000 CFM; the fan type of these AHU's is a plenum space with a capacity of 45,000 CFM. Each patient room will contain a VAV box with an average supply load of 760 CFM and an average return load of 660 CFM.Along with additional AHU's the roof will also see an addition of relief air plenum space. The roof will see an addition of seven new relief air plenums that have a capacity of 24,000 CFM.
The second floor mechanical space will not see much of an addition in terms of mechanical equipment; however, with the hospital expansion adding 6,500 SQFT of space to the second floor mechanial room, nearly half of that will serve as ventilation and a relief air plenum space of 4,110 CFM with louvers being place on the exterior.
Existing ductwork will be demolished and removed from the 70,000 SQFT of area to be renovated. New ductwork and piping will be designed for both the renovation and expansion. |
Electrical |
Along with the additional mechanical loads comes added electrical loads. A total of three Doubled Ended Switchgears and one Medium Voltage Switchgear will be added to the hospital in order to support the new power and lighting loads of the hospital expansion along with future hospital expansions. Included with the new power requirments within the patient rooms, a new bank of elevators is being added to the hospital, which is considered to signifcantly add electrical loads.
The south end of the existing hospital will receive two new pieces of switchgear equpiment. One of the switchgears is a 3-phase Medium Voltage Switchgear (MVS) with a nominal voltage of 15,000 Volts (V) and a 1200 Amp (A) main bus. The feeder size for this MVS will be a 4" Conduit with 3 #2/O wires and 1 #1/OG wire. The second switchgear is a Double Ended Switchgear which is identical with respect to voltage, ampage, and phase requirements as the other two Double Ended Switchgears. The primary of this switchgear is 3-phase with 12470 V, 3 wires, a 600 A main bus, and a 40,000 AIC Rating. The secondary of this switchgear is also 3-phase with 480/277 V, 4 wires, a 4,000 A main bus, and an 85,000 AIC Rating. Along with one of the Double Ended Switchgears being added to the south end of the existing hospital, one will be added to the east end of the existing hospital and the third will be placed in a designated area on the mechanical 2M floor.
The new equipment was supported by the power distribution that spanned from the South and East end of the existing hospital via a ductbank in the ground floor. |
Lighting |
As each patient floor was repetive, so is the ligthing plan. The patient rooms were calculated to require an average of 41.0 footcandles (fc) with minimum of 13.2 fc and a maximum of 60.8 fc. Two direct/indirect linear fluorescent luminaires are called out to be installed above the patient beds. A surface mounted linear fluorescent color changing uplight luminaire is also called out to be installed above the dresser/closet space in each patient room. Each patient bathroom contains a linear fluorescent parabolic downlight. Each T5HO lamp required for these fixtures will consume 54 Watts (W).
The corridors needed an average of 20 fc, which led to 1'x4' recessed direct/indirect luminaires typically being used in the hallways and corridors. |
Structural |
The superstructure is composed of a structural steel system with cast-in-place concrete floors. The structural system consists of typical 'W' beams that will tie into the existing structure with W10 x 12 beams and moment connections. The exterior framing also utilizes moment connections and includes W14x22 and W24x131 beams, where the interior framing is mainly comprised of shear connection with W12x14 and W12x6 beams. Concrete walls are not present in the new addition as the weight of the building will be carried by the steel exterior framing.
Before structural steel can proceed, a number of existing columns need to be reinforced in the hospital to ensure a stable new structure will work properly with the existing structure. The new steel will be welded into the existing columns, creating moment connections.
The floor system will consist of 4 1/2" lightweight concrete poured over 2" gauge galvanized deck making the total slab thickness 6 1/2". The new patient bathrooms have been design with a 4" depressed slab to allow space for the plumbing and fixtures within the room. |
Fire Protection |
The fire protection system includes a wet-pipe sprinkler system throughout the new addition. The renovation area will also be fitted with the new sprinkler system. This system consists of automatic sprinklers attached to piping containing water that is connected to a water supply. These sprinklers are opened when heat melts a fusible link. The minimum spray density for this system in patient room is .20 gallons per minute (gpm) over a 1,500 sq. ft. area; with light hazards, the spray density is .10 gpm over 1,500 sq. ft. The maximum allow protection area per sprinkler for patient rooms is 225 sq. ft. meaning that every 225 square feet of space in a room must have at least one sprinkler head. |
|
|